The building industry is responsible for the consumption of approximately 40% of the total energy in our world. In Europe, this industry is responsible for 32% of the CO2 emissions and 25% of the generated waste every year! A big part of this energy and these CO2 emissions is due to the manufacturing of concrete. Besides, the production of concrete leads to irreversible environmental damages on river beds and on sea coasts. Indeed, a huge amount of sand have to be extracted from theses areas and this resource is getting rarer and rarer, year after year. And yet our economy cannot do without it. Concrete is the number one building material that is used in almost all construction projects. It’s time to use greener alternative! Let’s see how to produce greener concrete for our buildings.
Why do we use so much concrete?
In a city like Shanghai, concrete is the main building material. In this city, concrete constitutes on average 40% of residential buildings. This percentage goes up to 46% for non-residential buildings.
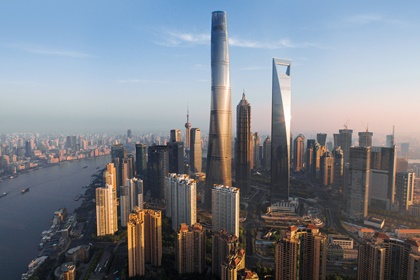
This is the first used material! But why do we use so much concrete in our buildings? That’s because concrete is a very strong and durable material. It can resist erosion and climate changes and requires very little maintenance. A building made of concrete will be safe. There is no risk the walls burn and no air volatile organic compounds are released into the air (if there is no organic additive in it).
Moreover, concrete can be molded into various forms and it can be easily reinforced with steel rods, wires, meshes and cables.
But how is produced concrete concretely?
You need four elements to produce concrete: water, sand, gravel and cement. The recipe is the following: 1 volume of cement, 2 volumes of sand, three volumes of gravel and half a volume of water. You mix all of this and wait for it to dry and you have concrete!
Unfortunately, producing cement is very energy intensive. The production of clinker, the main constituent of cement is responsible for about 5% of greenhouse gas emissions in the world!
To produce clinker you have to crush limestones and clays. The homogenized mix is then brought to approximately 1450°C in a calcination furnace. Then, the clinker must be cooled and crushed again (heating the mixture has created aggregates). But the crushed limestone releases a lot of CO2 during calcination, and a lot of coal of fuel is used to heat the mix up!
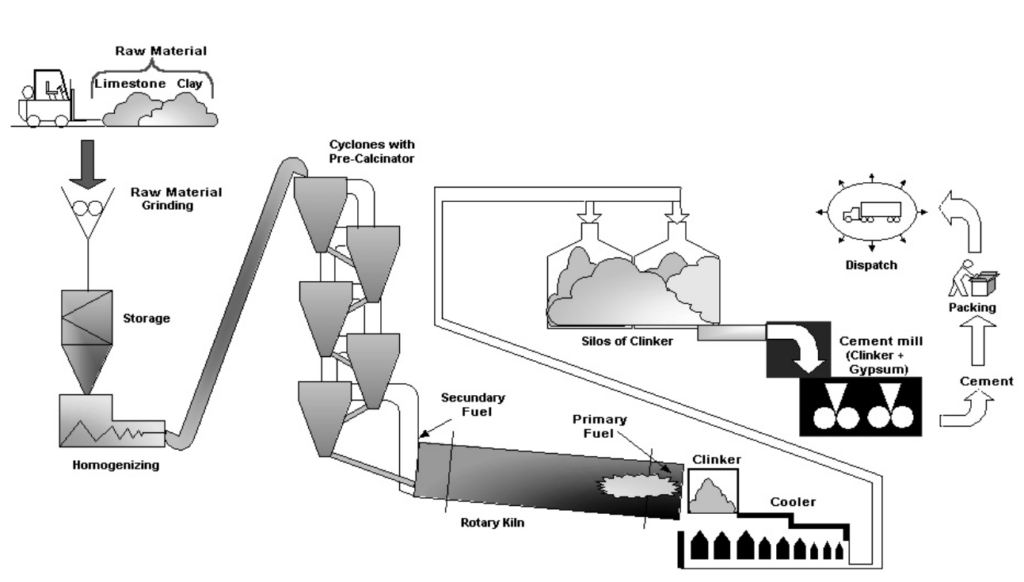
Sand is also required to make concrete. But sand is starting to lack from the river beds and the coasts all around the world! Besides, extracting sand has an important negative impact on the environment, such as the coastal erosion. What about desert sands? This is unfortunately not really a good alternative.
Concrete has a large climate impact and there is an increasing demand of it everywhere. It is now time to develop more sustainable solutions for the construction industry. It is time to learn how to produce greener concrete for our buildings.
So how to produce greener concrete for our buildings?
Actually, it is already possible to produce concrete with zero emission of CO2. In 2014, some Japanese researchers developed a new concrete called CO2-SUICOM (CO2 Storage under Infrastructure by Concrete Materials). To produce this new concrete, a special additive (dicalcium silicate) is used as well as coal-ash, to reduce the amount of cement used.
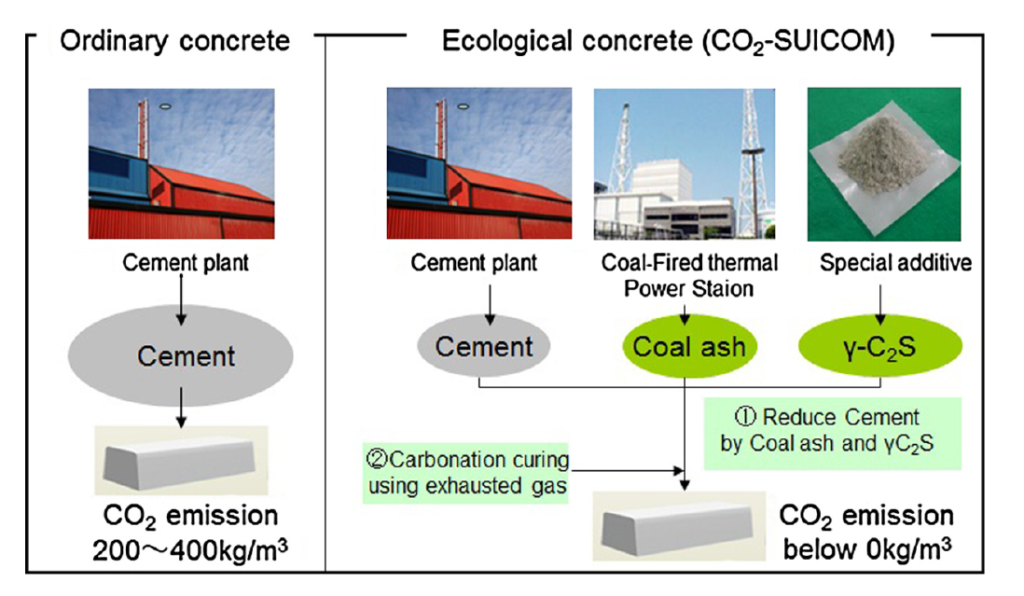
And once manufactured a large amount of CO2 can be captured by this concrete. In order to capture the CO2, the concrete has to be placed in a chamber and the gas has to be injected. Then, the concrete absorbs the CO2 in its structure. As a result, the total amount of CO2 produced is zero and can even be negative. Another advantage of this approach is the use of industrial by-products such as coal-ash to replace cement.
The bio-cementation is another interesting approach to reduce the CO2 emissions. In 2019, researchers proposed to use bacterial metabolism in the production of cement. The clinker production step is replaced by a biologic limestone dissolution and recrystallization.
They named this zero CO2 emitting cement the BioZEment (ZE for Zero Emission). Based on the life cycle analysis, they pretend that one ton of concrete made of BioZEment emits 70 to 83% less CO2 than conventional concrete. And it would be possible to get better results with a better optimization.
According to the researchers, we can already produce concrete with a considerably reduced climate impact thanks to BioZElement. But the large-scale use mainly depends on public acceptance-related factors.
In other studies, novel clinkers such as sulfoaluminate cements and magnesia cements proved to replace efficiently traditional cement clinker.
And what about sand?
Natural sand can be replaced by manufactured sand. Manufactured sand is produced by crushing rocks. Rocks can be found everywhere, contrary to river-quality sand. And you understand it, these machines should be powered with renewable energy! Otherwise another source of greenhouse emission gas is created.
Among the recent trends to replace natural sand there is: copper slag, granulated blast furnace slag, washed bottom ash, quarry dust and recycled construction and destruction waste.
Copper slag
Copper slag is a by-product of copper extraction. Rather than being just a waste, this by-product can have a different use in the building industry. Actually, about 33 million tons of copper slag is generated in the world every year. And natural sand can be replaced up to 50% by copper slag in the concrete mix without strength and durability losses.
Granulated blast furnace slag
Granulated blast furnace slag is a by-product from the steel industry. This by-product can be used as a replacement to natural sand up to 75 per cent (recommended). Actually, if we mix copper slag and granulated blast furnace we could replace 100% of the natural sand of the concrete mix. However, the authors noticed a slight “bleeding” tendency in this case and thus recommend a 80%-20% mix.
Washed Bottom Ash
Bottom ashes are produced by coal thermal power plants. About 20% of the ash produced during the combustion of coal are bottom ashes, the rest is fly ashes. Bottom ashes are heavy ash that does not rise in the air. This kind of by-product has less use in the industry. But we can use it to reduce the amount of natural sand in the concrete mix.
Researchers showed that up to 30% of the natural sand can be replaced by washed bottom ash in the concrete mix.
Quarry dust
In quarries, about 25% of the total production is left out as waste material-quarry dust. This waste could be used to replace natural sand in the concrete mix as suggested by researchers (link above). The replacement can be up to 75% of the natural sand, and it could even be total, if combined with coal fly ash!
Construction and Destruction waste
The construction industry generates a lot of waste and this poses an environmental challenge. These wastes should be minimized by the reuse and recycling it. Up to 50% of natural sand can be replaced with this recycled waste and without degrading the strength and durability of the final concrete.
Foundry sand waste
For one ton of produced iron or steel casting, one ton of foundry sand is required. Foundry sand is used to prepare casting molds. In the USA, 9 to 13.6 million tons of foundry waste is generated every year by the steel industry. Alike the other mentioned by-products, managing this the foundry sand waste is a serious problem. Using it in the building industry would clearly be a win-win situation.
This waste foundry sand can actually be used as a replacement of natural sand as well. In 2019, researchers discovered that a certain type of foundry sand could help produce high quality concrete. This concrete has similar or even better characteristics than the regular concrete when used as full replacement.
To conclude
Having greener buildings require having greener building materials. We need building materials that does not harm the environment during their production. Concrete, mainly because of cement, is the number one polluting building material. Researchers are actively working on greener alternatives to the very polluting Portland cement. We already have some good options on the table. Some of these new approaches may need more tests to be fully industrializable, it true. But it is also true that we already have concrete alternatives we can use in the building industry, today. In fact, the biggest issue might be the general public acceptance of these new techniques.
Sand, another component of concrete, is in shortage. Besides, extracting natural sand is very destructive for river-beds and the surrounding environment. Today, we can already use by-products to reduce the amount of natural sand required to produce concrete. For some researchers, a full replacement is even possible in some cases.
If you’re an entrepreneur working in the building industry, you now know there are tangible alternatives to cement and sand. You now know how to produce greener concrete for our buildings. These alternatives are better for our earth and can also help you stand out from the crowd. And if your thing is net zero buildings, why not use green concrete to build them?
I would be happy to read your suggestions in the comments to make this article more useful for you! And if you notice a dead link or an outdated information, please let me know!
Bye!